Adinkra in Ntonso-Ashanti, Ghana
Adinkra cloth was originally only used as a mourning cloth. Today
it is also worn on other special occasions. The Boakye family demonstrates, teaches, and sells
Adinkra cloth in Ntonso. For a
demonstration, to buy Adinkra, to arrange for a class, or for more information, please
contact Peter Boakye in Ntonso-Ashanti, Ghana, West Africa. |
|
|
|
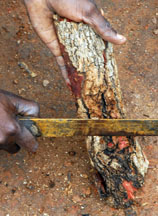 |
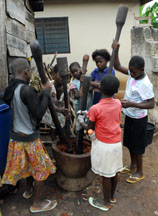 |
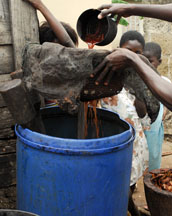 |
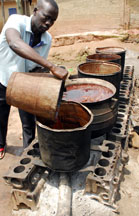 |
ADINKRA ADURO MEDIUM: To make adinkra aduro medium (colorant), the bark
and roots of the Badie (Adansonia digitata) tree are harvested, the outer
layer is cut away, then the inner bark is broken into pieces and soaked in
water for 24 hours. It is then pounded for about 3 hours in a wooden mortar,
boiled for several hours in water over a wood fire, strained
through a plastic window screen, then boiled for 4 more hours. |
 |
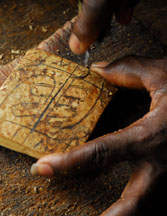 |
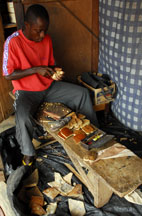 |
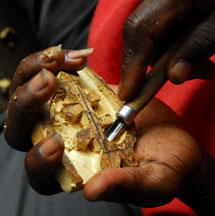 |
CALABASH STAMPS: The inside of a dry, thick-skinned calabash
is covered with shea butter for a year to slightly soften it. Then Paul Nyamaah Boakye (telephone: 024345516 and
0243167605) cuts off a piece with a knife, scrapes the outer skin with a knife, draws the pattern
onto it with a pencil, then carves away the negative space with a gouge. Paul carves
more than 70 different symbols, each of which represents a proverb, belief,
or philosophy. |
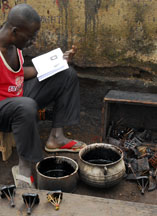 |
 |
 |
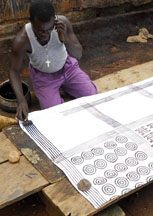 |
ADINKRA CLOTH PRINTING: Wooden planks resting on blocks
were covered with a 1" thick piece of foam rubber. Several symbols (which have
specific meanings) were chosen from an Adinkra chart, then the late Gabriel Boayke selected the stamps and
Anthony Boakye decided their placement on the cloth. After the starched shedder cotton fabric
(with a luster finish) was folded and laid on the foam rubber,
small nails were driven through the edges of the cloth with a rock.
Rocks were also placed along the edges of the cloth to keep it in place. A
comb (whose tangs were wrapped with nylon cord to help pick up the colorant) was
dipped into the adinra duro, then pulled across the cloth freehand to delineate
the sections to be printed. Although it requires practice and concentration,
expert printers are able to talk on a cell phone and converse with
onlookers while printing. |
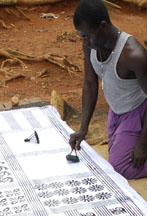 |
 |
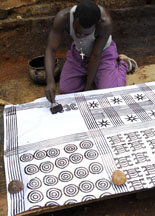 |
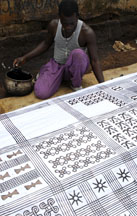 |
Following tradition, Anthony filled each section with
the same design. Before the section was actually printed, he figured out the placement by dry stamping
over the cloth. The stamp was then dipped into the adinkra duro and then the excess
was shaken off before bringing the stamp to the cloth. |
 |
 |
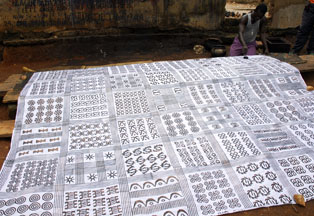 |
One edge of the loaded curved stamp was placed onto the
cloth, it was rocked across to the other edge, then it was lifted and dipped
into the colorant once again to repeat the procedure. |
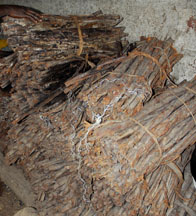 |
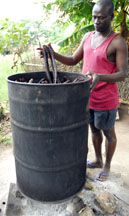 |
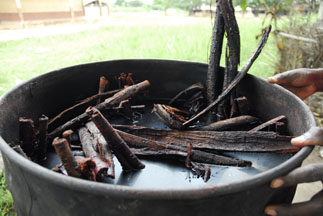 |
 |
Black cloth dye is prepared by soaking
Kuntunkuni (Bobax brevicuspe) bark and roots in a 50 gallon drum of water for
a few days, then boiling them over a wood fire, then beating the bark with a pipe,
then boiling them again until the liquid is very black. |
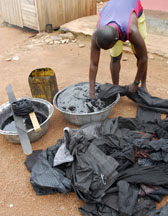 |
 |
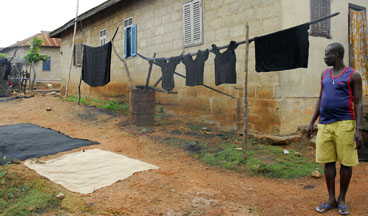 |
Faded cloth that needs to be refreshed along
with new cloths are dipped several times into the powerful dye, then left outside
to dry. |
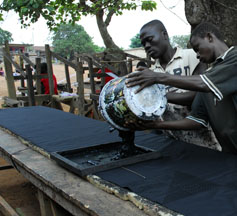 |
 |
 |
 |
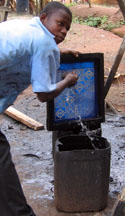 |
SCREEN PRINTED ADINKRA CLOTH: Instead being decorated with Adinkra stamps,
some cloth is screen printed in Ntonso with
images adapted from traditional Adinkra stamps. They are drawn by hand or on a
computer, transferred to a screen at a shop, then printed on a
foam rubber covered surface with water-based fabric paint. The screens are
cleaned with water after each use and reused many times. Here we see Kitiwa or Junior
(Opanin Yaw Boakye Junior) screen printing onto cotton fabric while kente strips are
woven in the background. |
A short version of
The Twenty-first Century Voices of the Ashanti Adinkra and Kente Cloths of Ghana paper
that I presented at the 2012 Textile Society of America Thirteenth Biennial Symposium, Textiles and Politics,
is included in the Proceedings as a pdf.
Links:
Ashanti Kente Weaving in Bonwire, Ghana
Ashanti Kente Weaving in Adawomase, Ghana
Ewe Kente Cloth Weaving in Denu, Ghana
Glass Bead Making in Odumase Krobo, Ghana
Ashanti Glass Bead Making in Daabaa, Ghana
Lost Wax Casting in Krofofrom, Ghana
Painting and Baskets of Sirigu, Ghana
Ga Coffins in Teshie, Ghana
THREAD, Inc. Organization
More Links:
Papermaking in Kurotani, Japan
Katazome (stencil dying) in Kyoto, Japan
Shibori in Kyoto, Japan
Batik of Java and Bali, Indonesia
Ikat Weaving in Bali
Printing in China
Batik in Cameroon
Backstrap Woven Ikat in Mexico
Footloomed Woven Ikat in Mexico
Web page, photographs, and text by Carol Ventura in 2008 & 2009.
Please look at Carol's home page to see more about crafts around the world.
|